Warehouse automation has evolved from being a trend to a critical necessity for companies striving to stay competitive. Automated Guided Vehicles (AGVs) are at the heart of this transformation. But how do these technologies work, and what are their advantages and challenges?
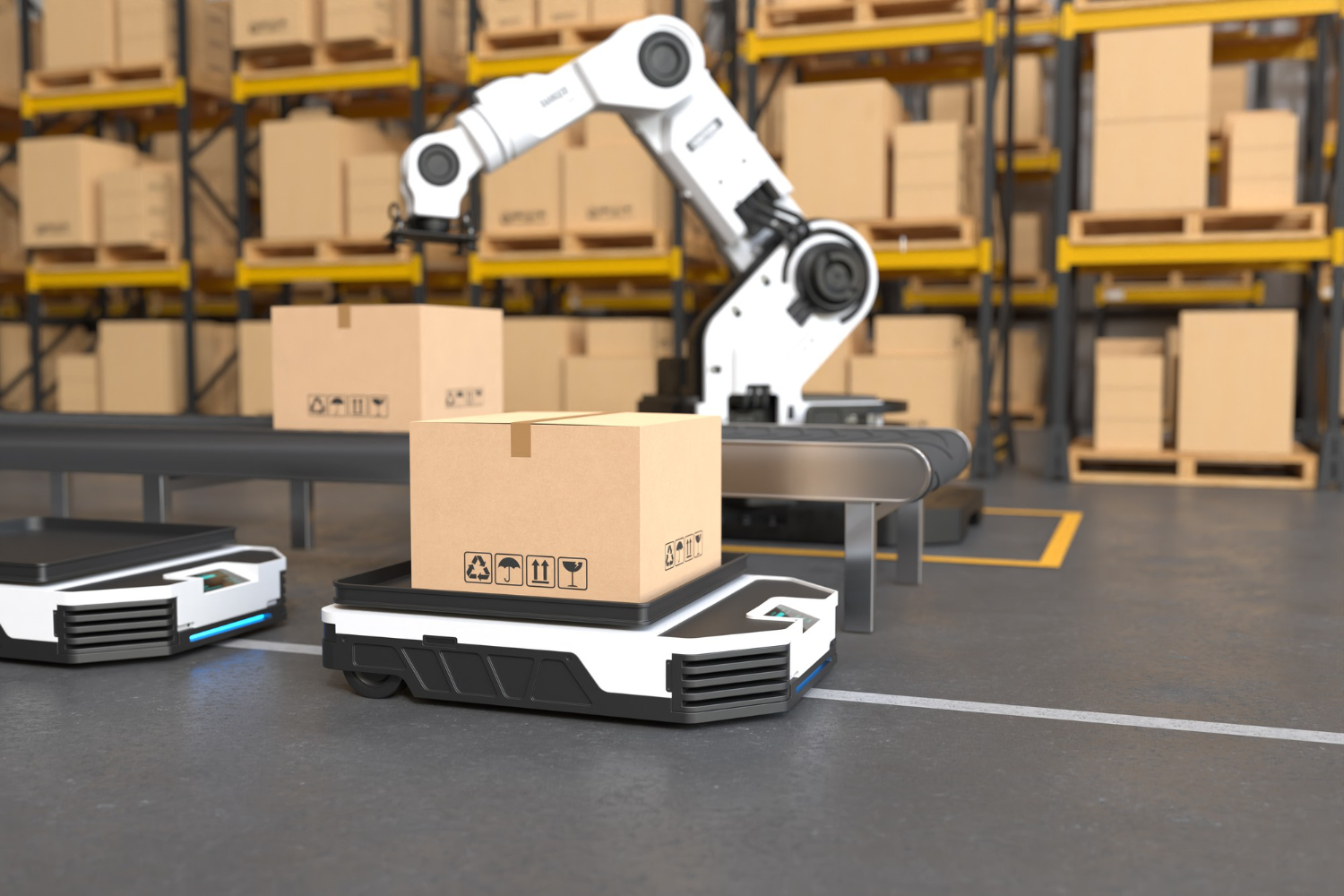
What Are AGVs and How Do They Work?
AGVs automate material flow processes within warehouses. They encompass not just the autonomous vehicles themselves but also the central control and communication systems that coordinate their operation. Together, they form a cohesive automation solution for logistics and intralogistics tasks.
AGVs rely on several advanced technologies, including:
- Sensors and cameras for precise navigation.
- AI-based algorithms to optimise routes and task priorities.
- Navigation systems such as SLAM (Simultaneous Localization and Mapping), RFID, or laser-based navigation for accurate positioning.
These vehicles carry out specific tasks, like transporting pallets or containers between storage locations, under the guidance of a centralised control unit. This control ensures smooth workflows, minimises errors, and maximises efficiency.
The Advantages of AGVs
- Constant Availability:
AGVs operate 24/7 without breaks or fatigue. Inductive charging ensures they remain functional even during brief downtimes.
- Error Reduction:
AGVs virtually eliminate transport damage and errors caused by human intervention through precise navigation and structured processes. - Flexibility
These systems adapt dynamically to changing warehouse requirements, optimising transport routes and task priorities in real time. - Enhanced Safety
Advanced sensors and navigation technologies significantly reduce accident risks in the warehouse, protecting employees and infrastructure. - Increased Efficiency
Centralised control ensures optimal use of resources, reducing idle times and enhancing overall productivity.
The Challenges of AGVs
- High Initial Costs
Implementing AGVs involves significant investment in vehicles, control software, infrastructure, and integration into existing systems. - Technological Integration
Many warehouses require customisation to become AGV-ready, ensuring seamless interaction with existing Warehouse Management Systems (WMS).
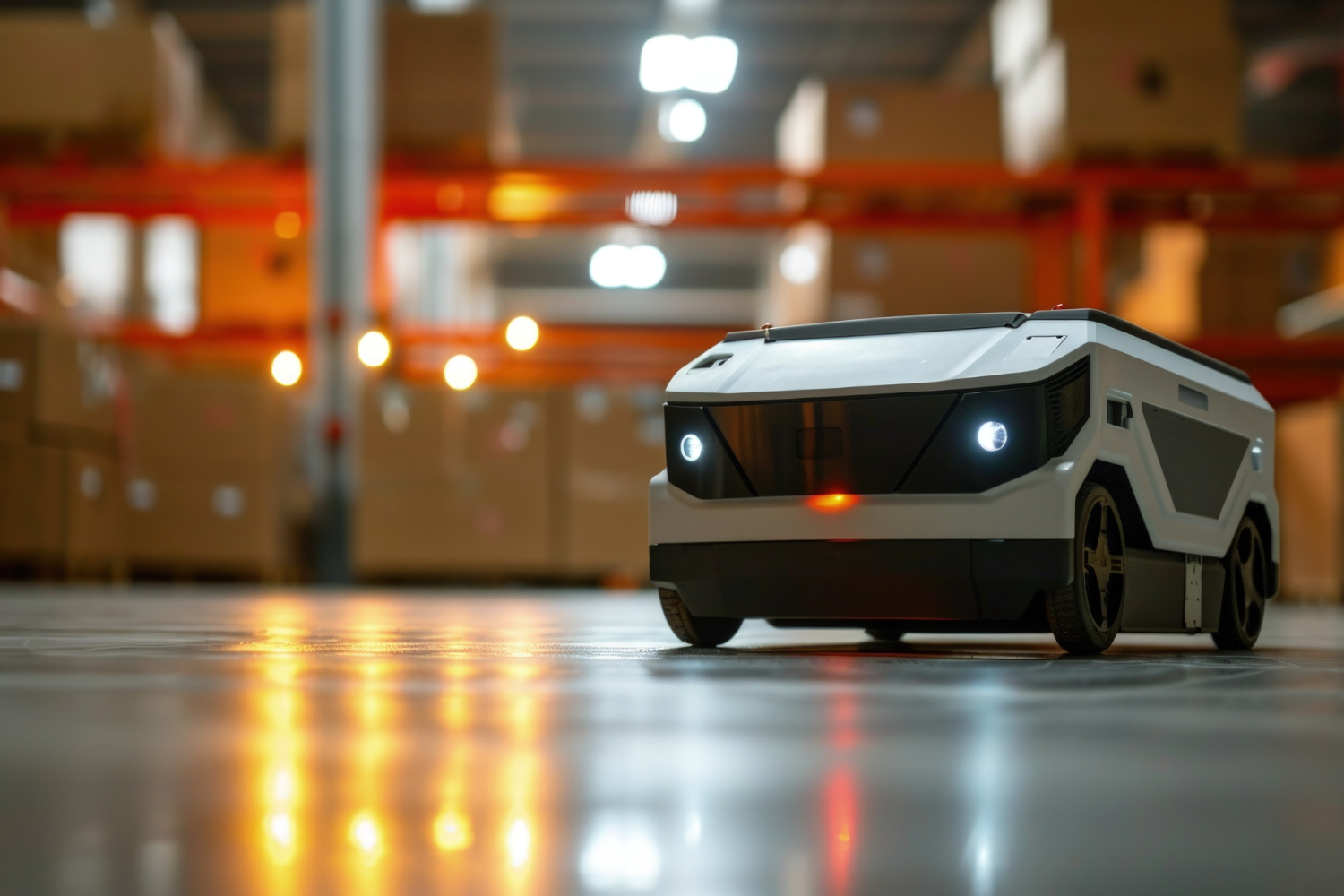
- Maintenance and Dependency
AGVs require regular maintenance and updates. Companies without internal technical expertise may depend heavily on external service providers. - Data Dependency
Accurate, real-time data is essential for AGV efficiency. Incomplete or incorrect data can disrupt operations.
When Are AGVs Worthwhile?
AGVs shine in large warehouse operations with high transport volumes and standardised processes. In these environments, their efficiency, accuracy, and constant availability lead to significant productivity gains.
For smaller warehouses or those with variable processes, hybrid or manual systems might offer greater flexibility and cost-efficiency.
Profitability Analysis: Making an Informed Decision
The decision to implement AGVs should be based on a detailed cost-benefit analysis, considering:
- Investment Costs
Initial expenses for purchasing vehicles, control systems, and infrastructure customisation. - Operating Costs
Maintenance, repairs, software updates, and energy consumption. - Savings
Reductions in personnel costs, accident-related expenses, and efficiency gains. - Amortisation Period Time required to recover the investment through returns.
- Operational Improvements
Gains in speed, capacity, and reliability.
Future Prospects
The evolution of AGV technology is accelerating. Innovations like IoT integration, self-learning algorithms, and enhanced navigation systems are poised to make AGVs even more efficient and user-friendly. These advancements will reduce training requirements and further improve their accessibility to businesses of all sizes.